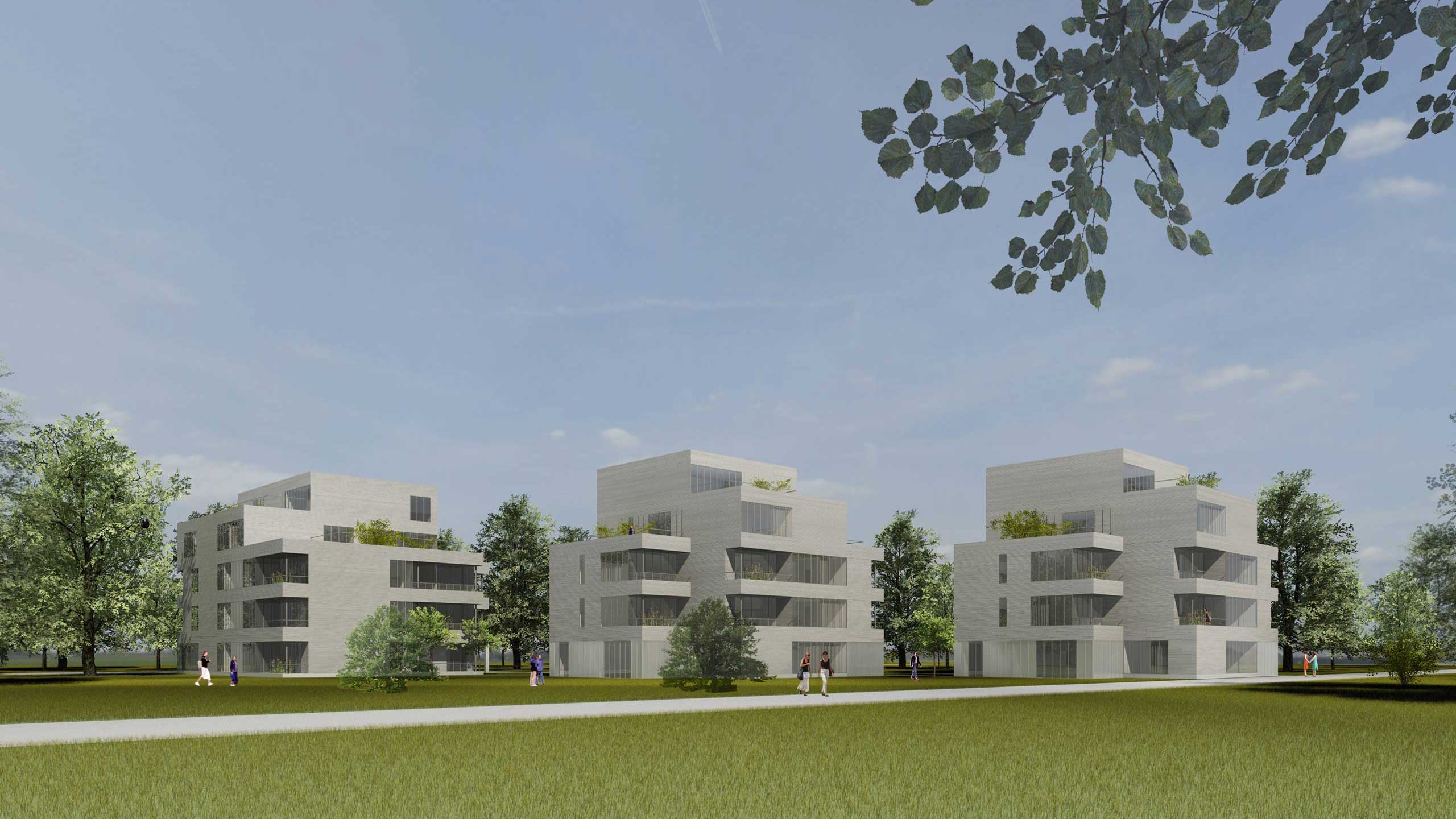
Urban Timber Construction Adlershof
Berlin
The building plot on the Adlershof Science Campus has a clear north-south orientation. It is developed on one side - via Newton-Straße. Access to the rear areas of the site must be via separate areas. On the NW side, the entire length of the site borders on a central green corridor, which already has high open space qualities. We therefore want to connect the private open spaces directly to the green corridor and keep the site as a whole largely free of car traffic.
A binding urban design defines a development figure consisting of 3 detached houses. This definition is rather unfavorable for the design parameters of development, A/V, 1st and 2nd escape routes. We are counteracting this with optimized utilization.
Development + outdoor facilities
The relationship to the neighboring natural space is extraordinary. We take these open space qualities as a benchmark and transform them into our own open space concept. The trafficable areas are reduced to a minimum. Cars are accommodated near the site access road and under the cantilevered upper floor of House 1. In this way, a large part of the site can remain open to infiltration and be linked to the landscape with lawns and water-bound paths.
Open spaces/garden areas for the private use of the house communities will have lawns, some with playground areas. This allows private open spaces to merge into the park landscape without any perceptible boundaries. In this way, an extensive connection to the landscape is created.
The entrances to the three buildings are easily recognizable and barrier-free on the ground floor. The vestibules are generously dimensioned and thus form places for conversation “en passant”. The surfaces of the stairwells are untreated - exposed concrete as an in-situ concrete construction with board formwork and, if necessary, a colored coating.
Buildings
“Density - privacy - resource” are the criteria according to which the buildings were developed. Balconies and direct access to open spaces with links to the public parks support this concept. The apartments and buildings are staggered in such a way as to prevent prying eyes. The houses stand freely on the site and do not have basements.
Construction
The load-bearing structure is a timber skeleton system. Wooden beams span over 5m in the longitudinal direction, hybrid ceilings (wood + steel) are laid across them with a span of up to approx. 7.5m.
This creates free floor plans - “plan libre” - that are permanently variable and can also be changed in the future with just a few simple steps. Only the positions of the installation shafts are fixed. The ceilings are installed as timber-StBn composite ceilings, the façades are suspended as timber frame elements in front of the load-bearing skeleton and clad with horizontally structured larch cladding.
This construction method enables extensive prefabrication - the primary supporting structure, ceilings and façades are constructed in the factory and assembled on site. This means that the construction time can be reduced to a minimum.
Data
Study
2017
Address
Newtonstraße/
Alexander-von-Humboldt-Weg
12489 Berlin
Client
HOWOGE Wohnungsbaugesellschaft mbH
House 1
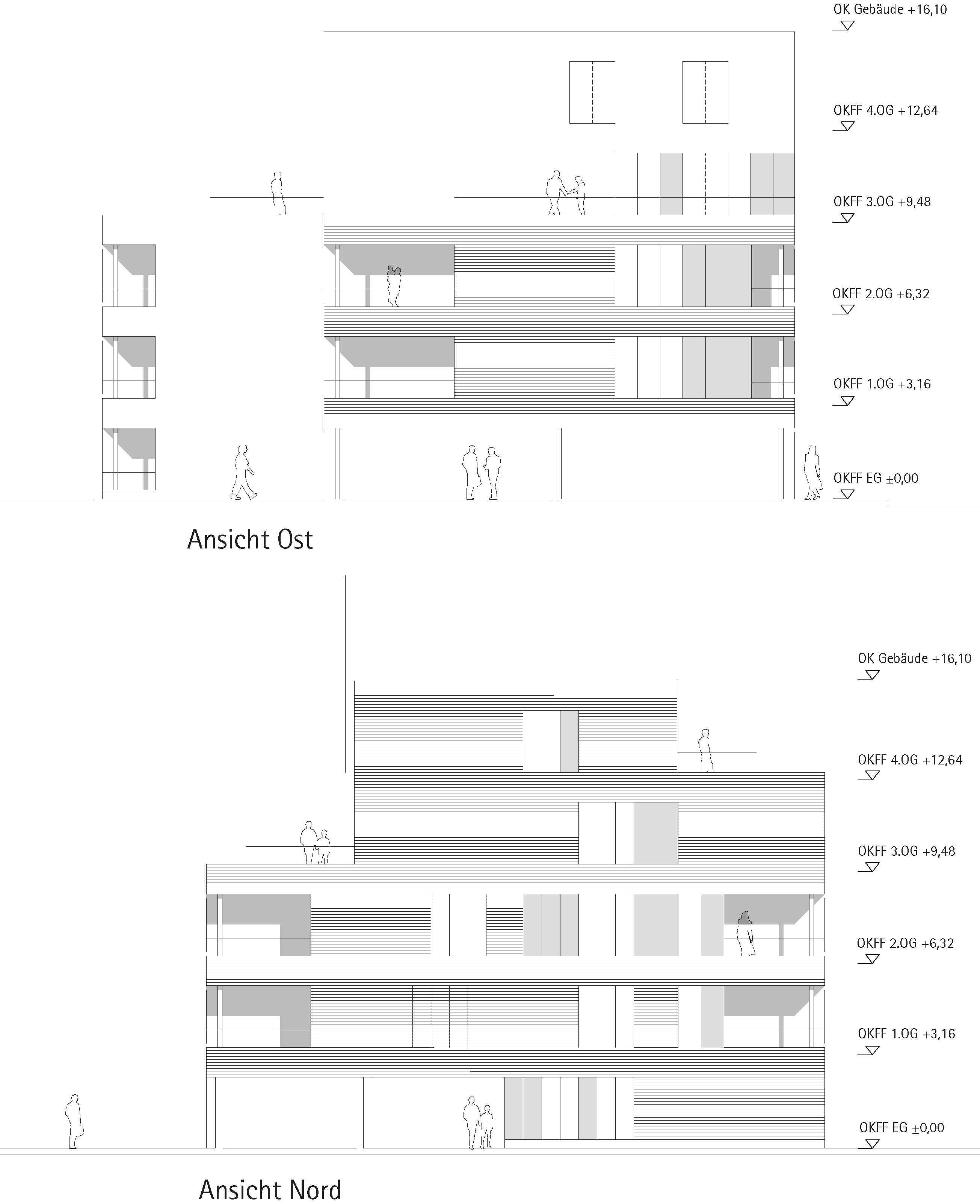
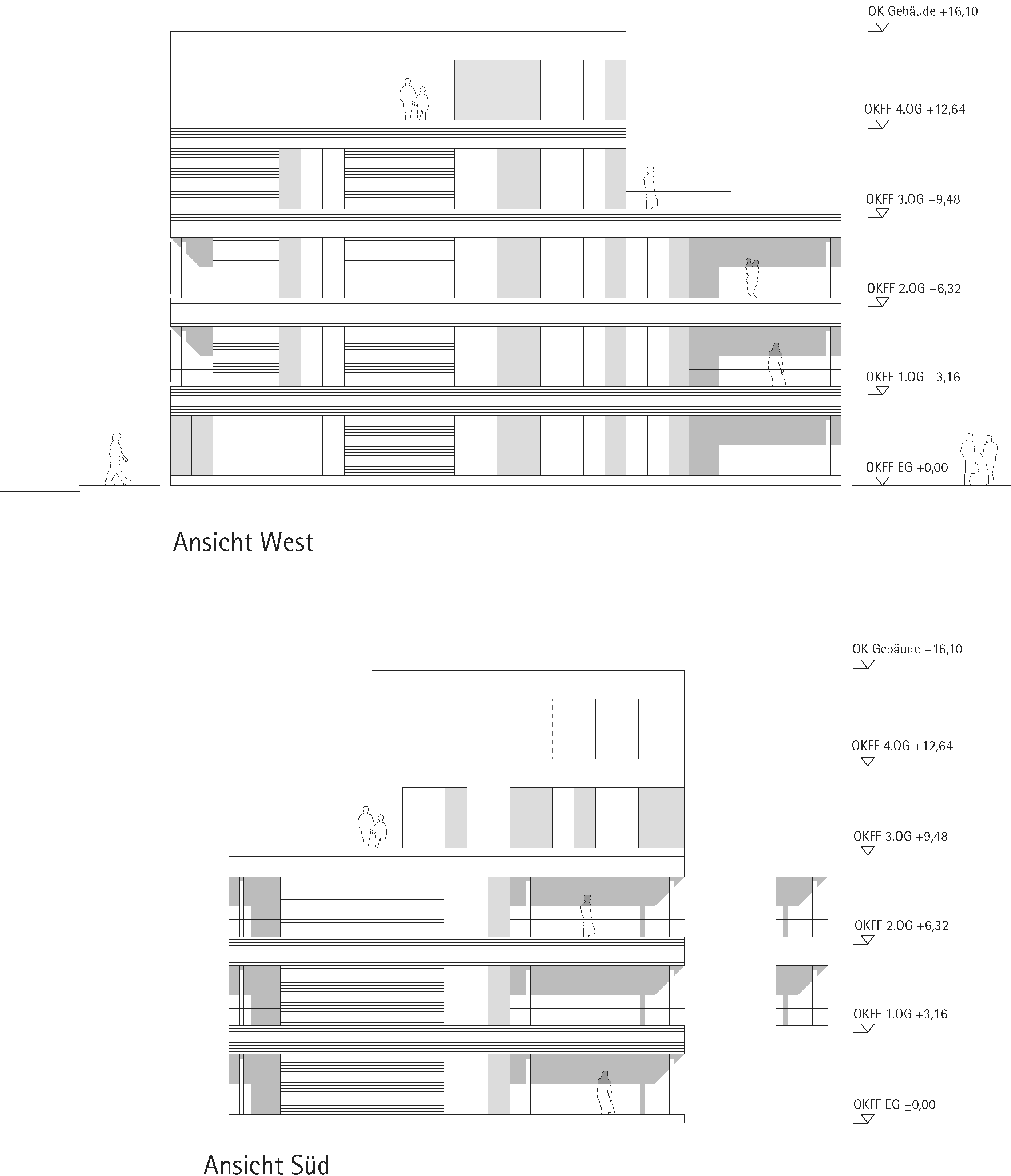
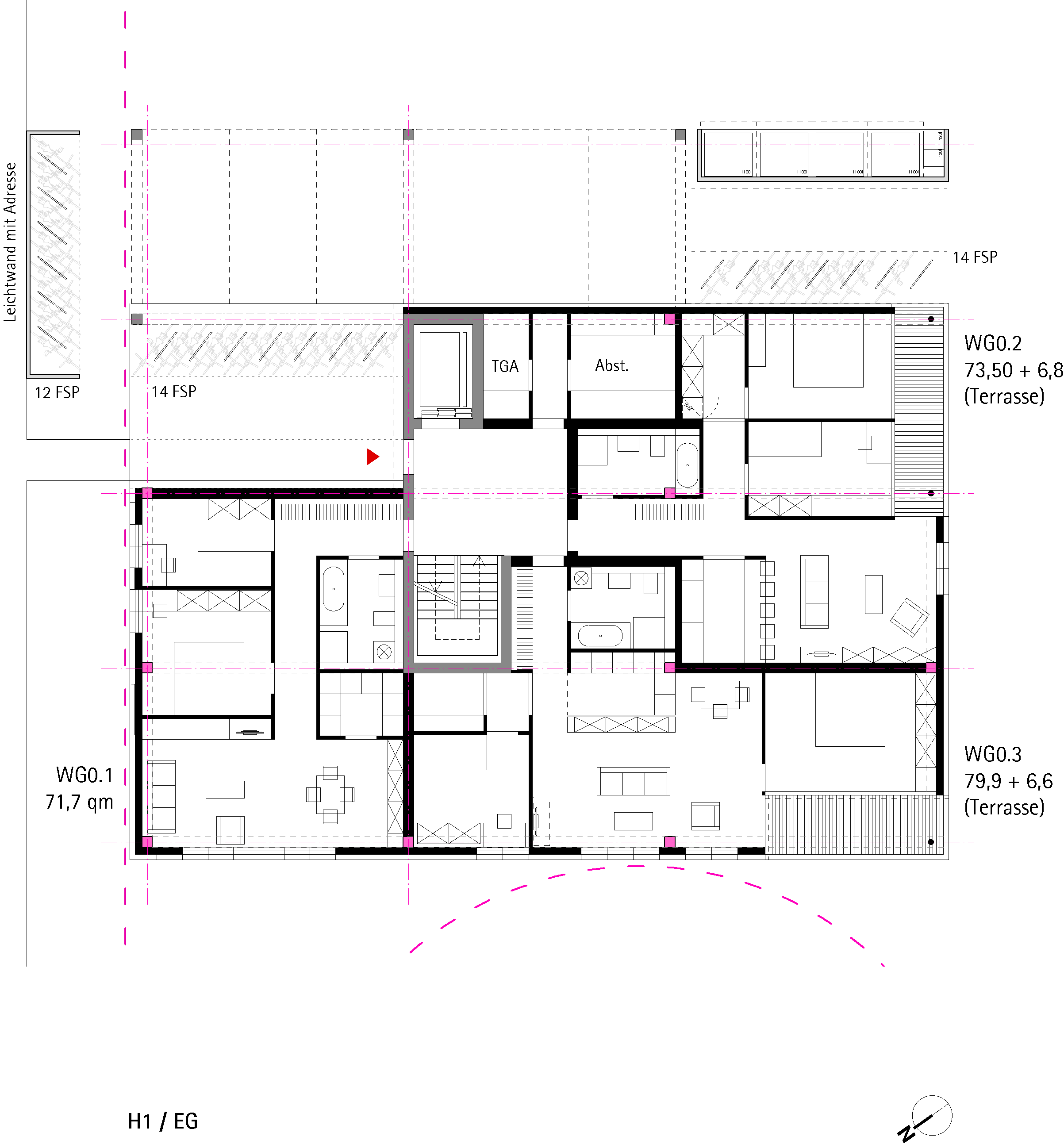
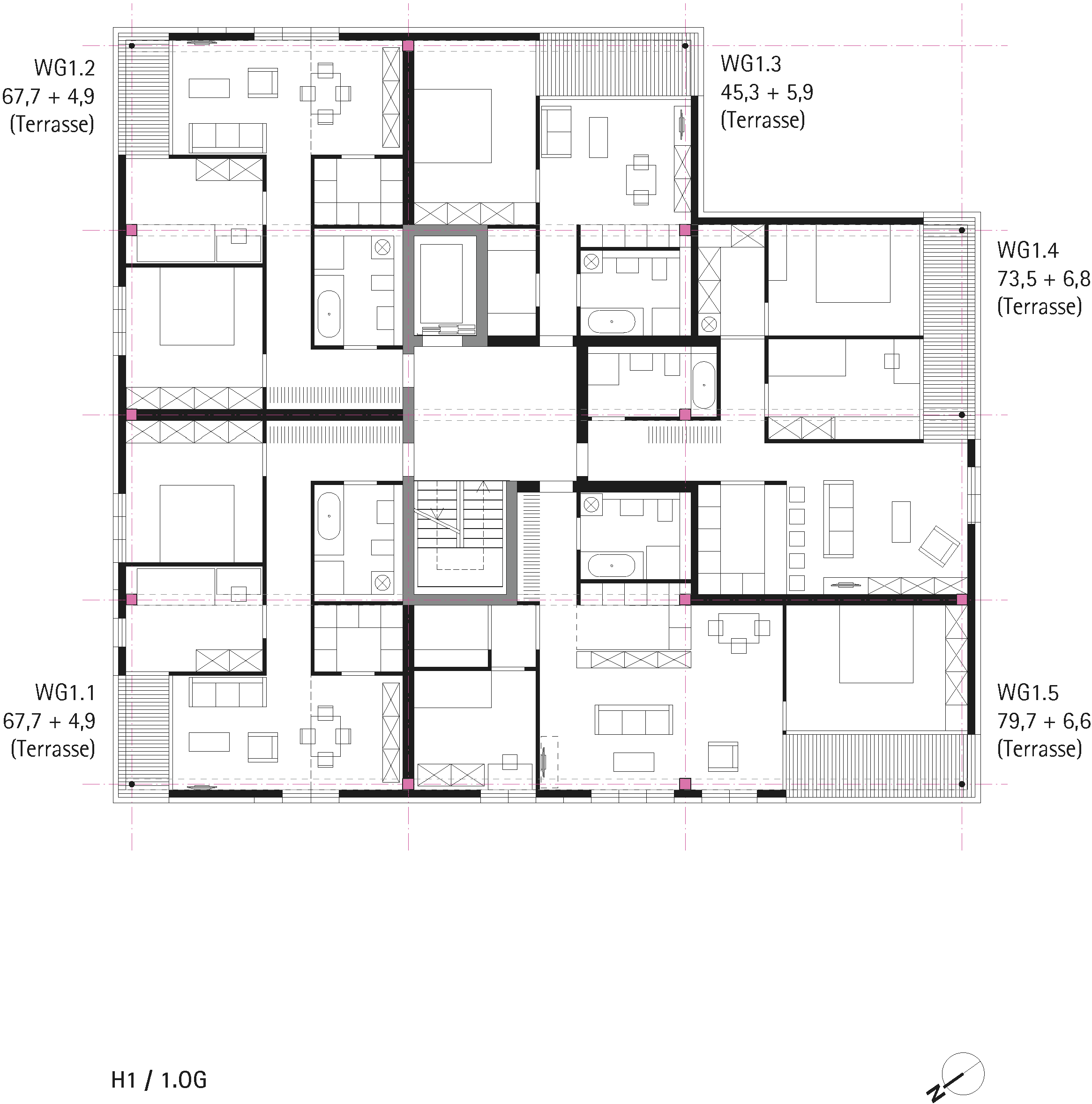
House 2 + 3
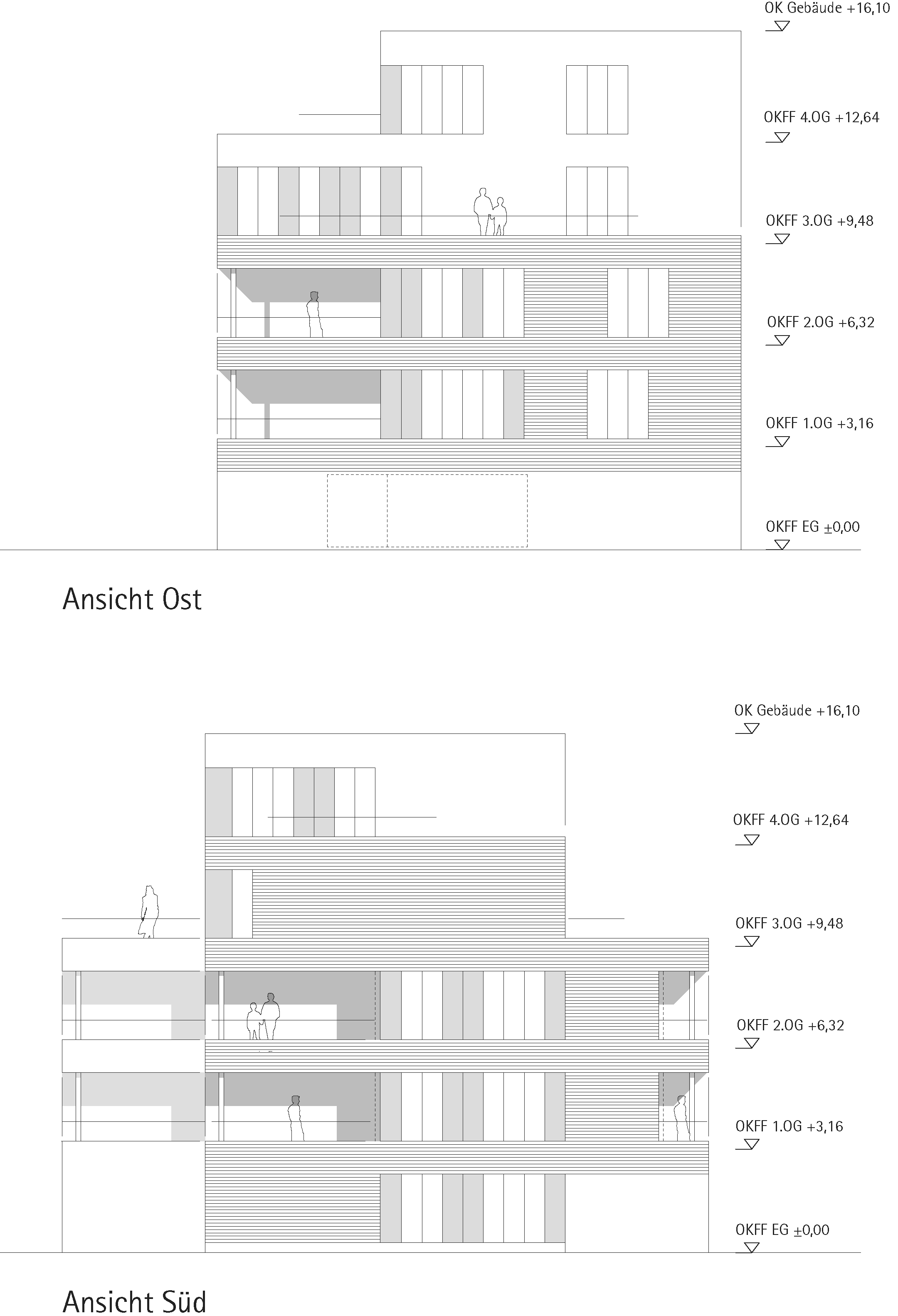
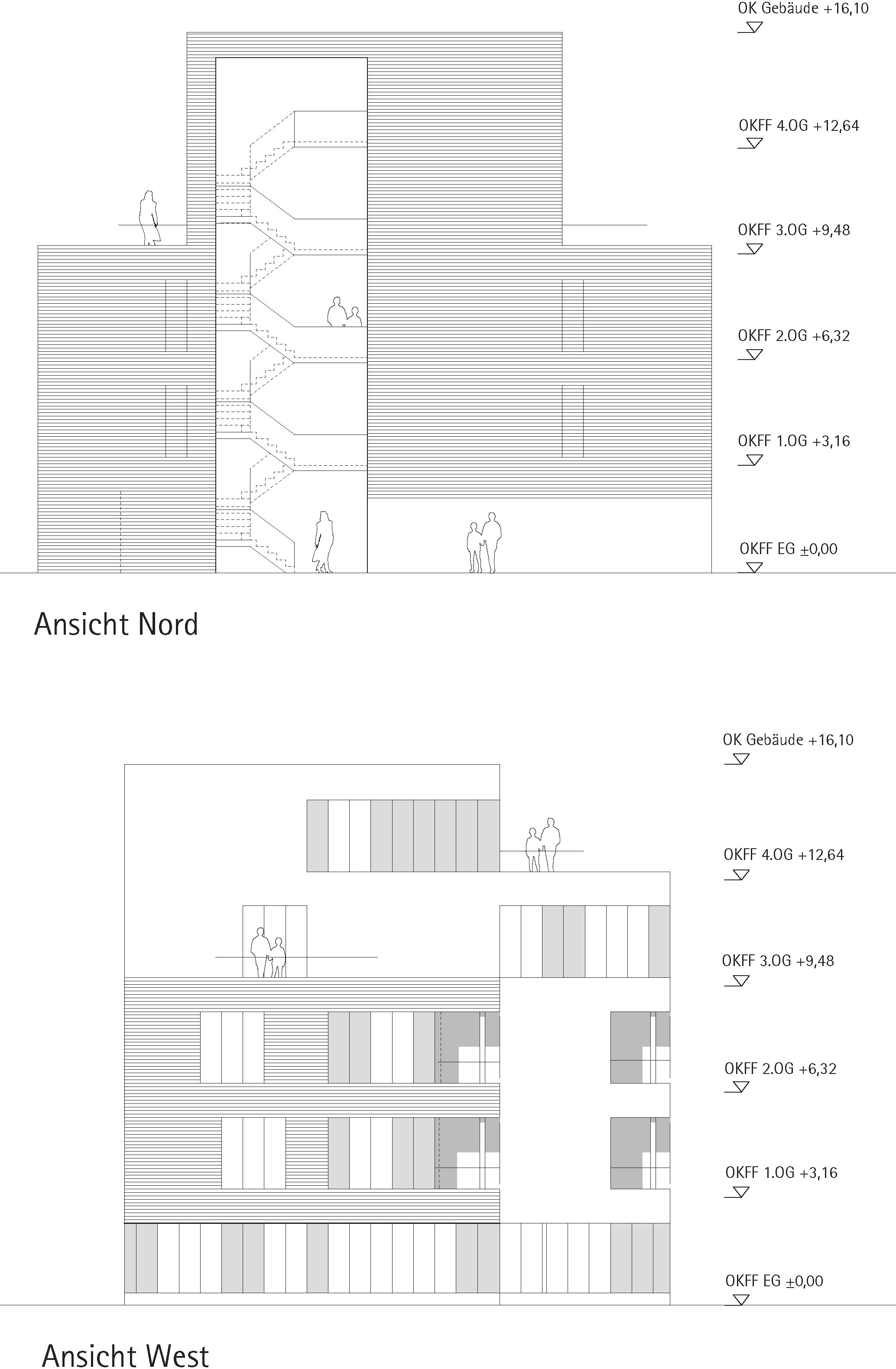
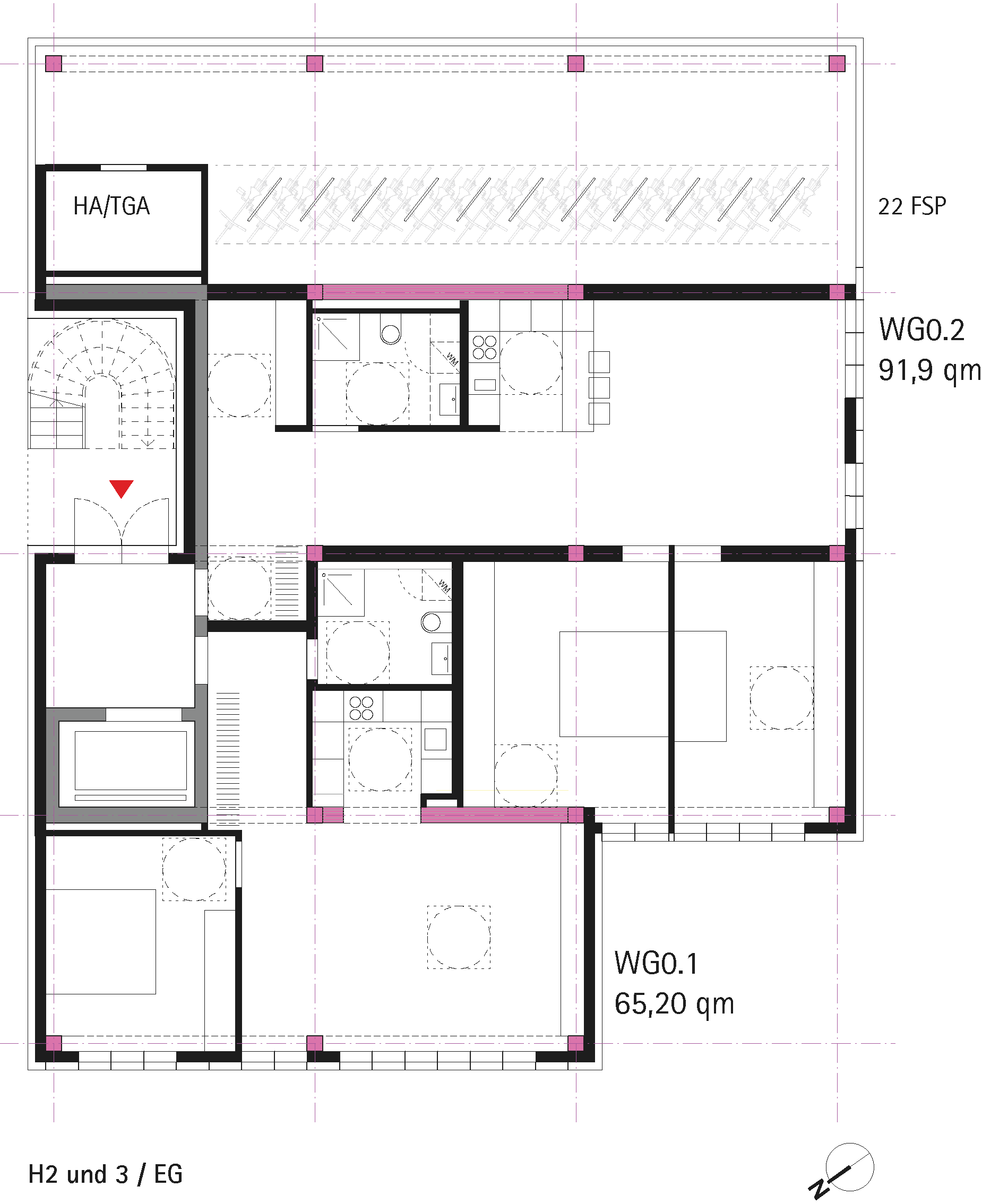
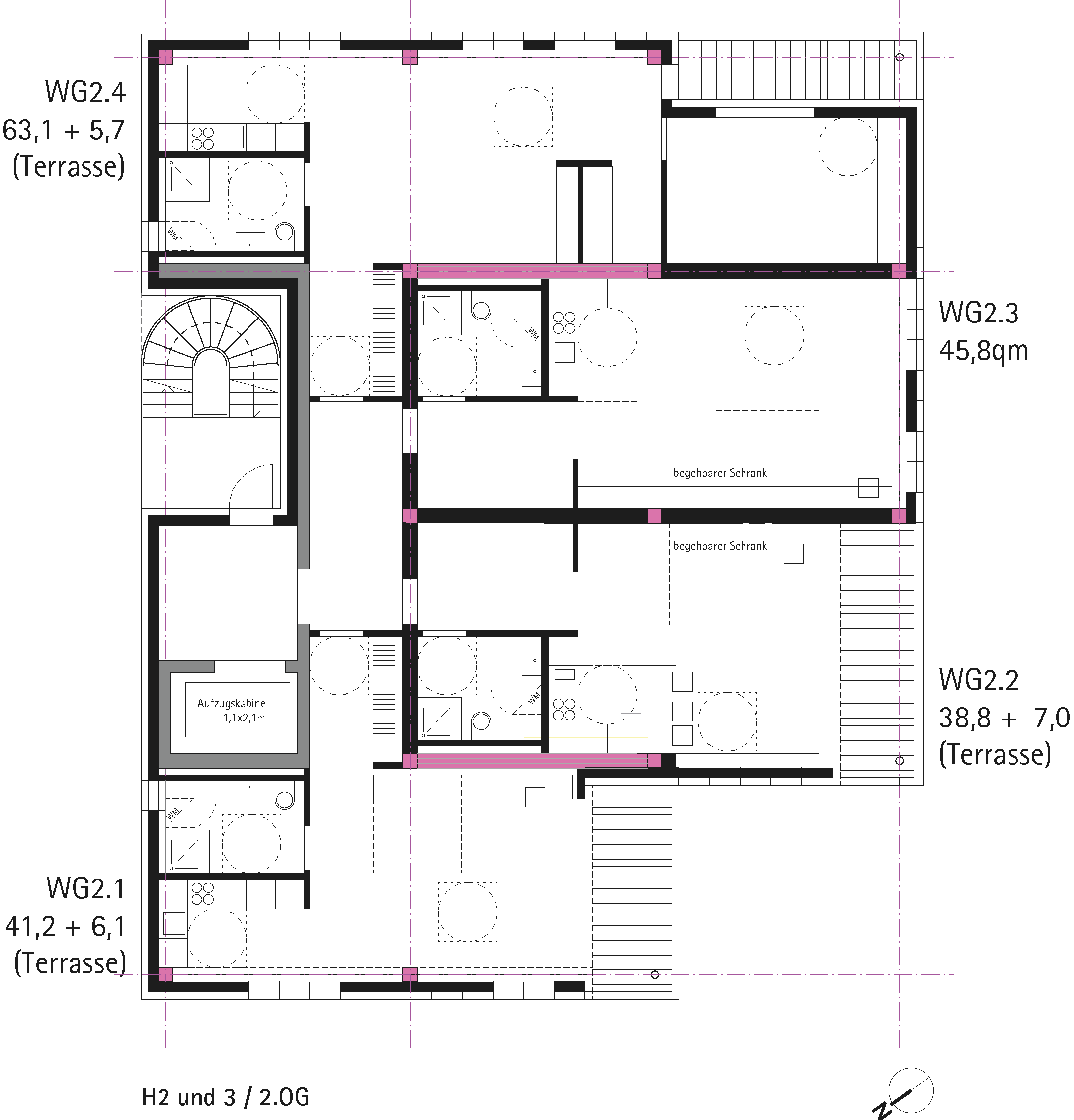