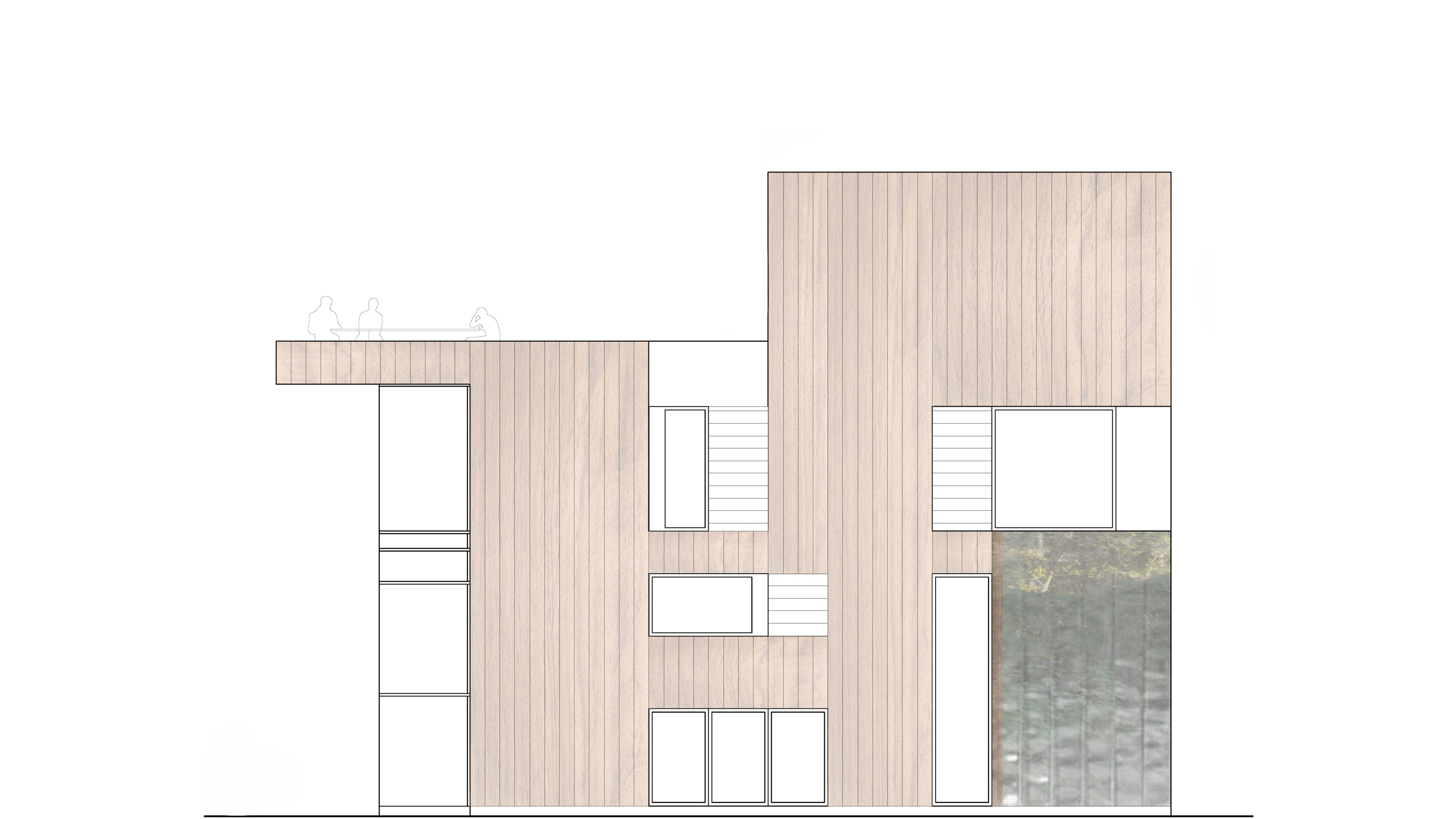
Spreestudio Clubhaus
Berlin
The new building will be positioned parallel to the adjacent water basin, ensuring protection of the landscape with an appropriate distance.
The building is expected to be used by 13 units. Four units on the ground floor will extend over a space height of approximately 5.60 meters, featuring a suspended gallery accessible via an internal staircase. Eight smaller units on the upper floor will be accessed via two stairwells. One stairwell core with sanitary facilities will extend to the roof and provide access to the top rental unit, a meeting room. The roof will be designed as a walkable area with intensive landscaping and will be accessible to all tenants.
The building will be constructed using a combination of wooden and reinforced concrete structures. Core areas inside and the floor slabs will be made of reinforced concrete, providing stability to the skeleton structure. Wooden columns and ceiling beams will be installed according to structural requirements and fire protection standards. The terrace and the meeting room on the roof will be constructed using a mixed wood and steel framework.
The façade construction will be made of wood with a metallic surface and will feature individual floor-to-ceiling window elements. The water side will be entirely constructed using a post-and-beam system with glass.
The interior fit-out will include only basic sanitary facilities and connections for a kitchenette in each rental unit. Flooring and wall surfaces will be finished by the tenants themselves.
The building will be constructed using a combination of timber and reinforced concrete structures. The internal cores and floor slabs will be made of reinforced concrete, providing rigidity to the skeletal structure. Wooden columns and ceiling beams will be installed according to structural requirements and fire protection standards. The terrace and the meeting room on the roof will be built using a mixed wood and steel construction.
The façade construction will be made of wood with a metallic finish and will feature individual floor-to-ceiling window elements. The waterside will be entirely constructed with a post-and-beam system using glass.
The interior fit-out will include only basic sanitary facilities and connections for a kitchenette in each rental unit. Flooring and wall surfaces will be finished by the tenants themselves.
Data
Study
2016
Address
Zur alten Flussbadeanstalt 1
10317 Berlin
Germany
Client
Spreestudios GmbH Co. KG
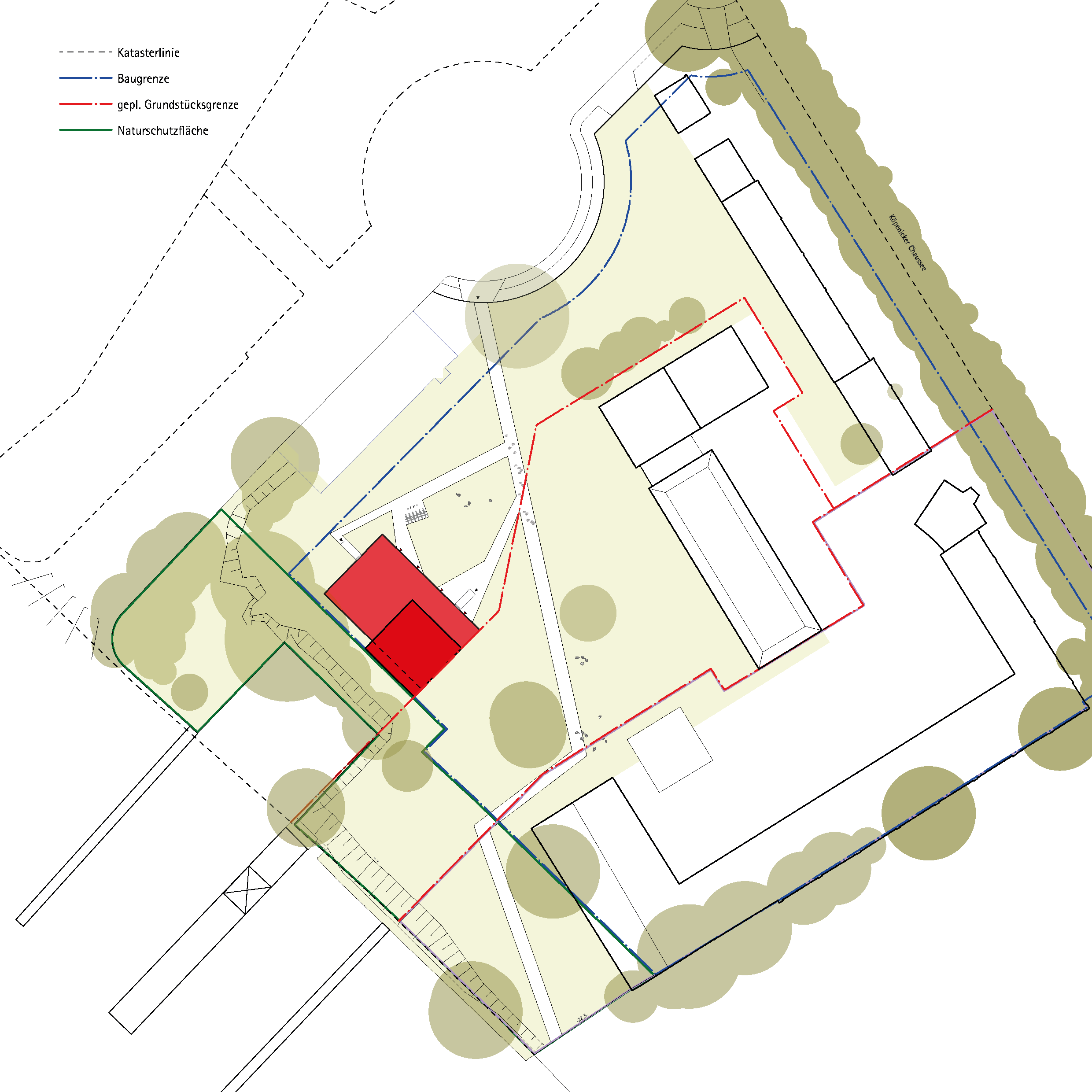
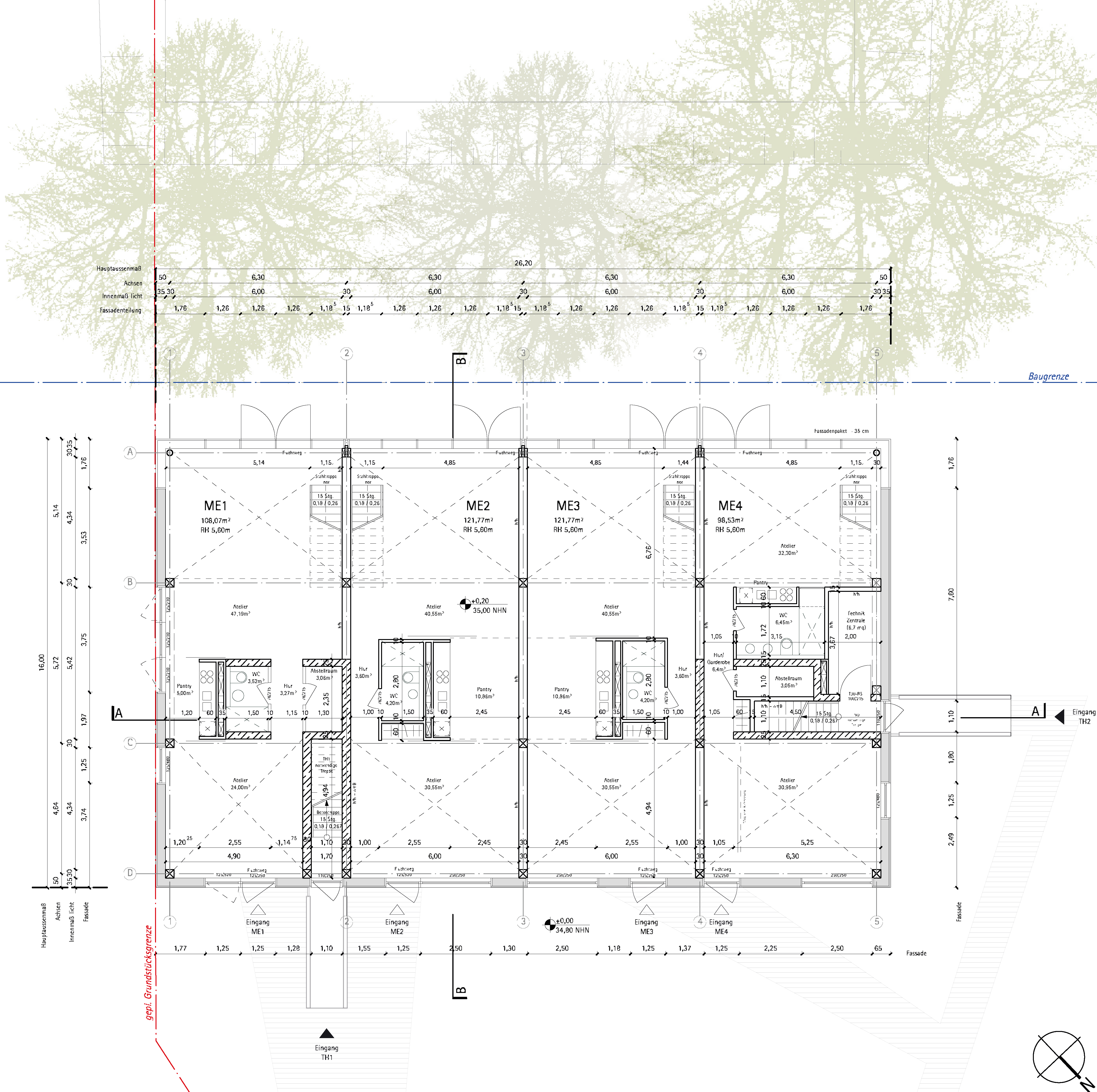
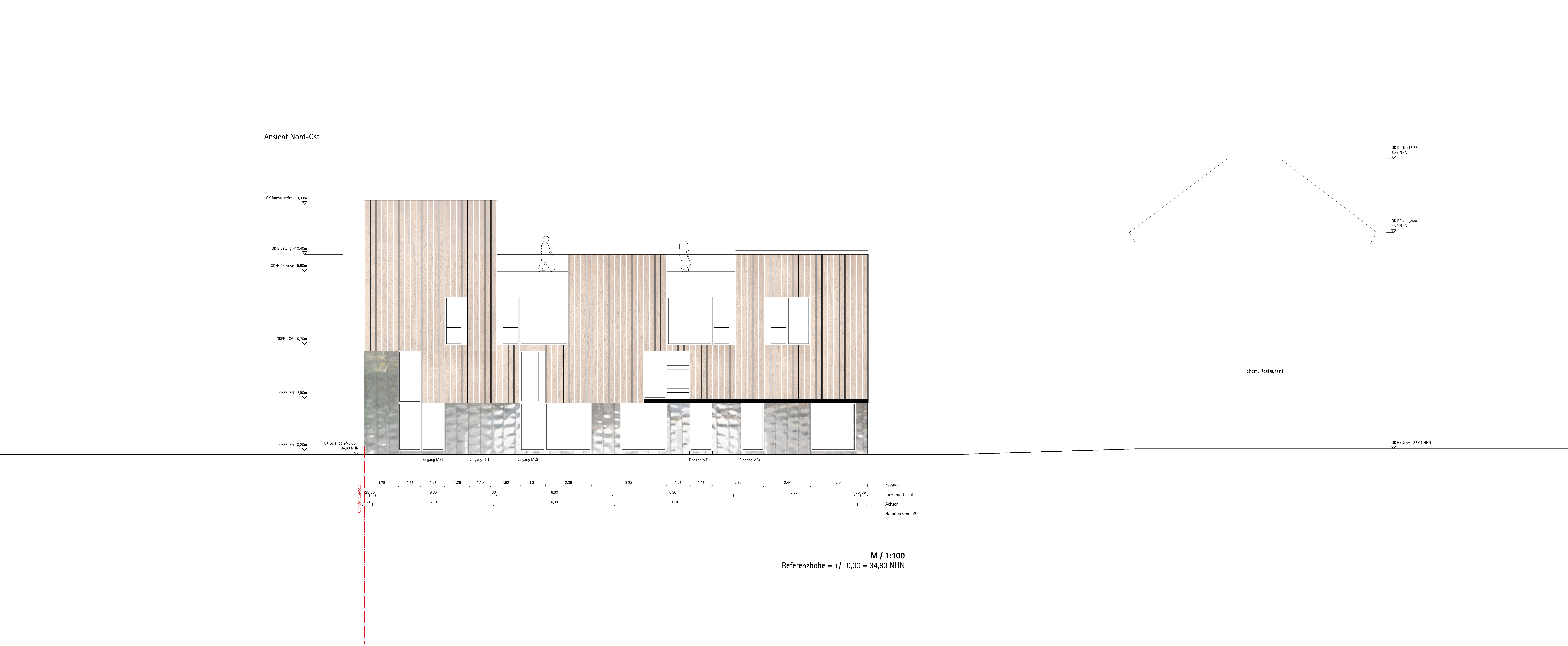
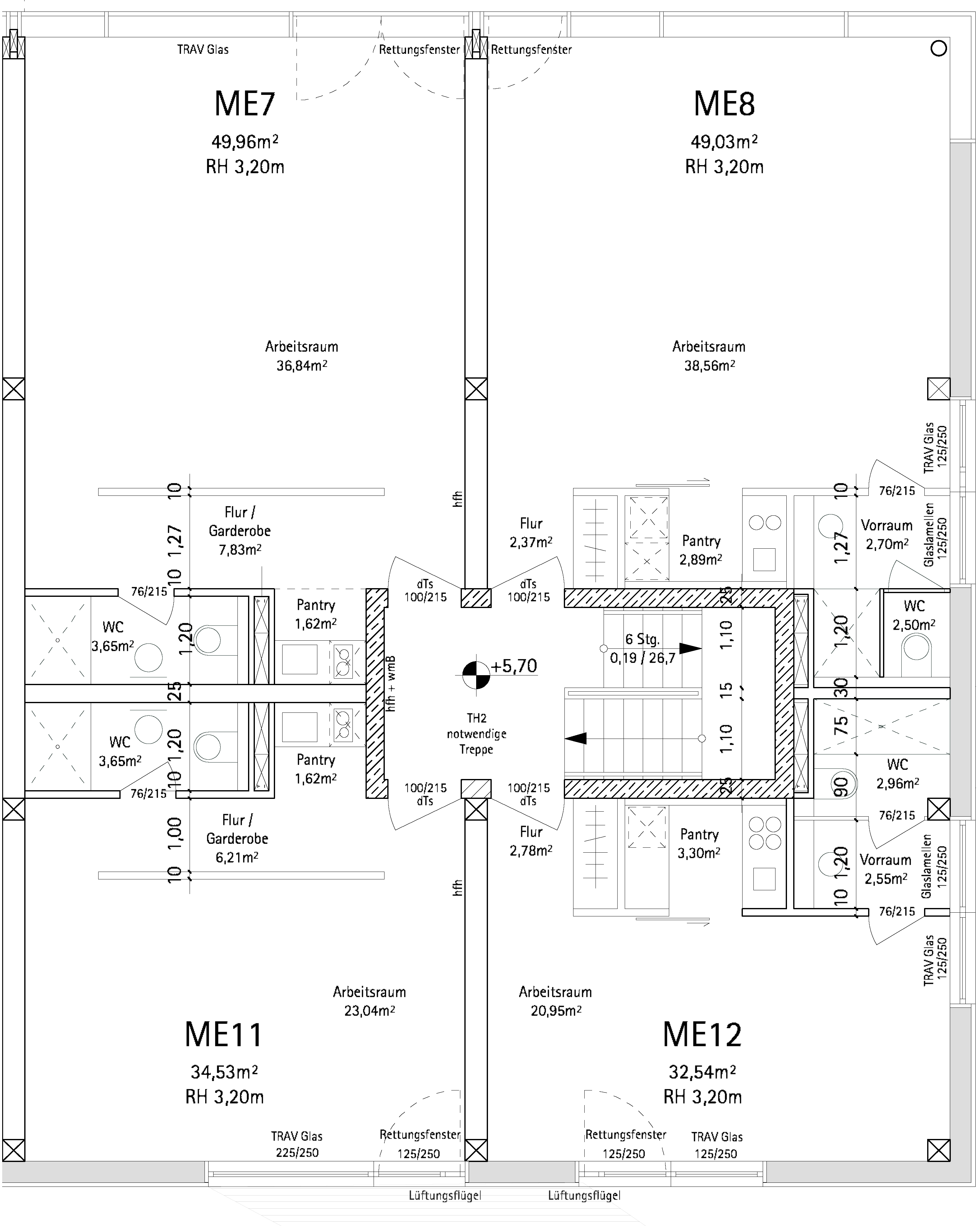
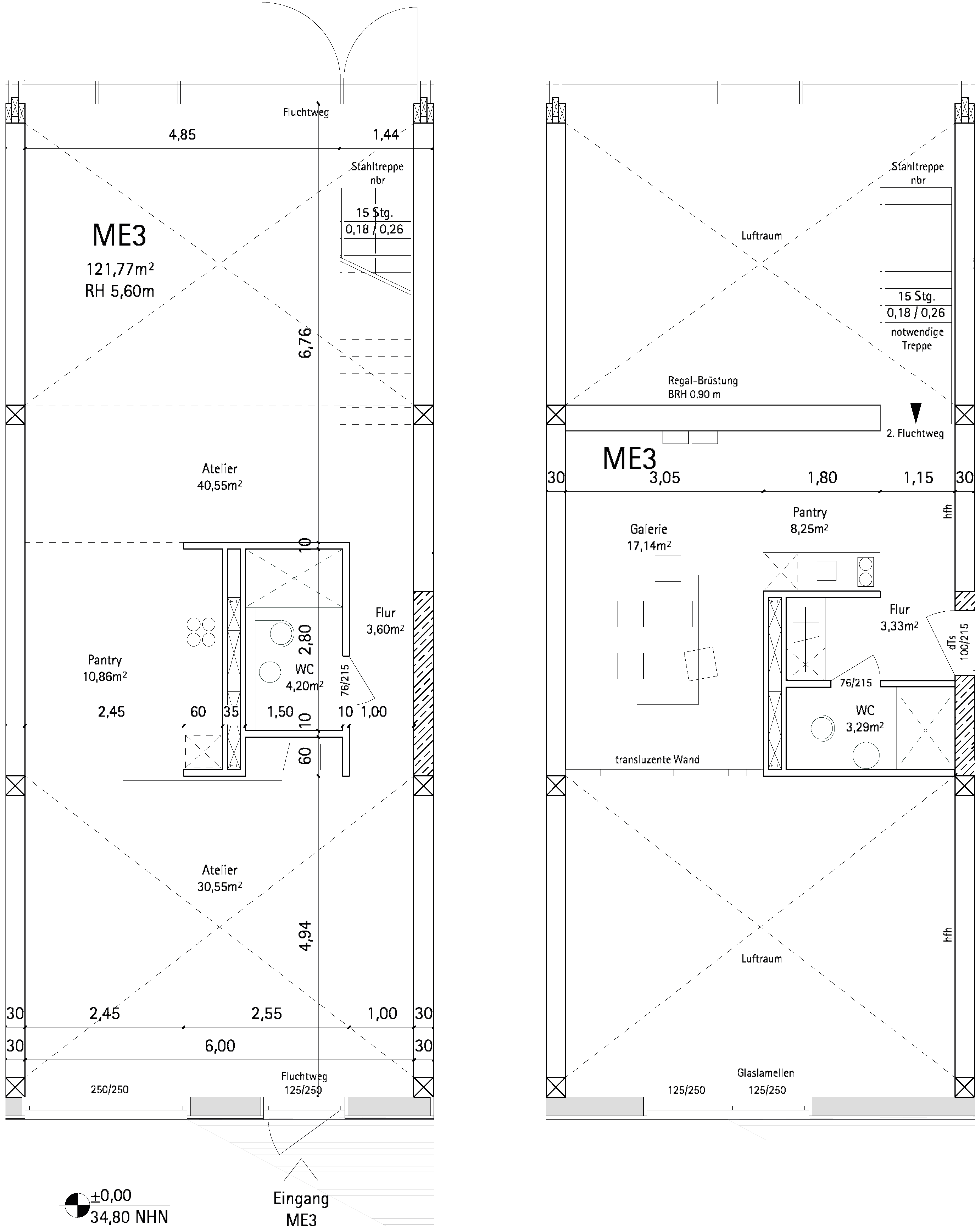